Please select your location and preferred language where available.
A massive, constantly evolving smart factory powered by three billion data points and AI: The Yokkaichi Plant of KIOXIA is at the forefront of flash memory innovation.
Laying the foundation for using data in our digital society
Reprinted from: EE Times.com / EE Times.eu
Reprinted from content published in EE Times.com / EE Times.eu on July 14, 2025
This content is used with permission from EE Times Japan.
Department names and titles are as of the time of the interview.
The Yokkaichi Plant of KIOXIA Corporation is located in Yokkaichi City, Mie Prefecture, one of Japan's leading industrial cities. In addition to being one of the world's largest flash memory facilities, the Plant is also a smart factory that has consistently introduced cutting-edge digital technology for the past 30 years. The Yokkaichi Plant manufactures state-of-the-art products by taking full advantage of AI technology and the 3 billion pieces of big data that the Plant generates daily, and it continues to further evolve through the use of digital-twin technology.
The massive smart factory uses data and AI to support flash memory production
As the rapid expansion of AI makes data more valuable than ever, the role of flash memory is becoming increasingly important. To make the best use of the AI technologies of machine learning, deep learning, and generative AI, collecting and analyzing data are essential. The demand for flash memory to store such valuable data, the starting point for all AI applications, grows in parallel with the rapid development of AI.
Flash memory is produced at the Yokkaichi Plant of KIOXIA Corporation in Yokkaichi City, Mie Prefecture.
Yokkaichi City, one of Japan's leading industrial cities, is home to a large petrochemical complex, as well as headquarters and factories of several corporations in the automotive, machinery, and food sectors. The KIOXIA Yokkaichi Plant, which was constructed in Yokkaichi City, is a massive factory whose area is equivalent to approximately 98 soccer fields (694,000 m2). Seven production facilities stand next to each other with thousands of manufacturing devices in their cleanrooms operating 24 hours a day under fully automated control. Since its establishment in 1992, the Yokkaichi Plant continues to expand in order to meet the increasing demand for flash memory associated with the development of applications; a new production facility (Fab 7) was completed in 2022, marking the 30th anniversary of the establishment of the company. The Yokkaichi Plant currently employs a total of approximately 10,000 people.
As one of the world's largest flash memory facilities, the Plant is also a smart factory powered by cutting-edge digital technology. State-of-the-art manufacturing is carried out by taking full advantage of AI technology and the 3 billion data points generated every day from every section of the production lines.
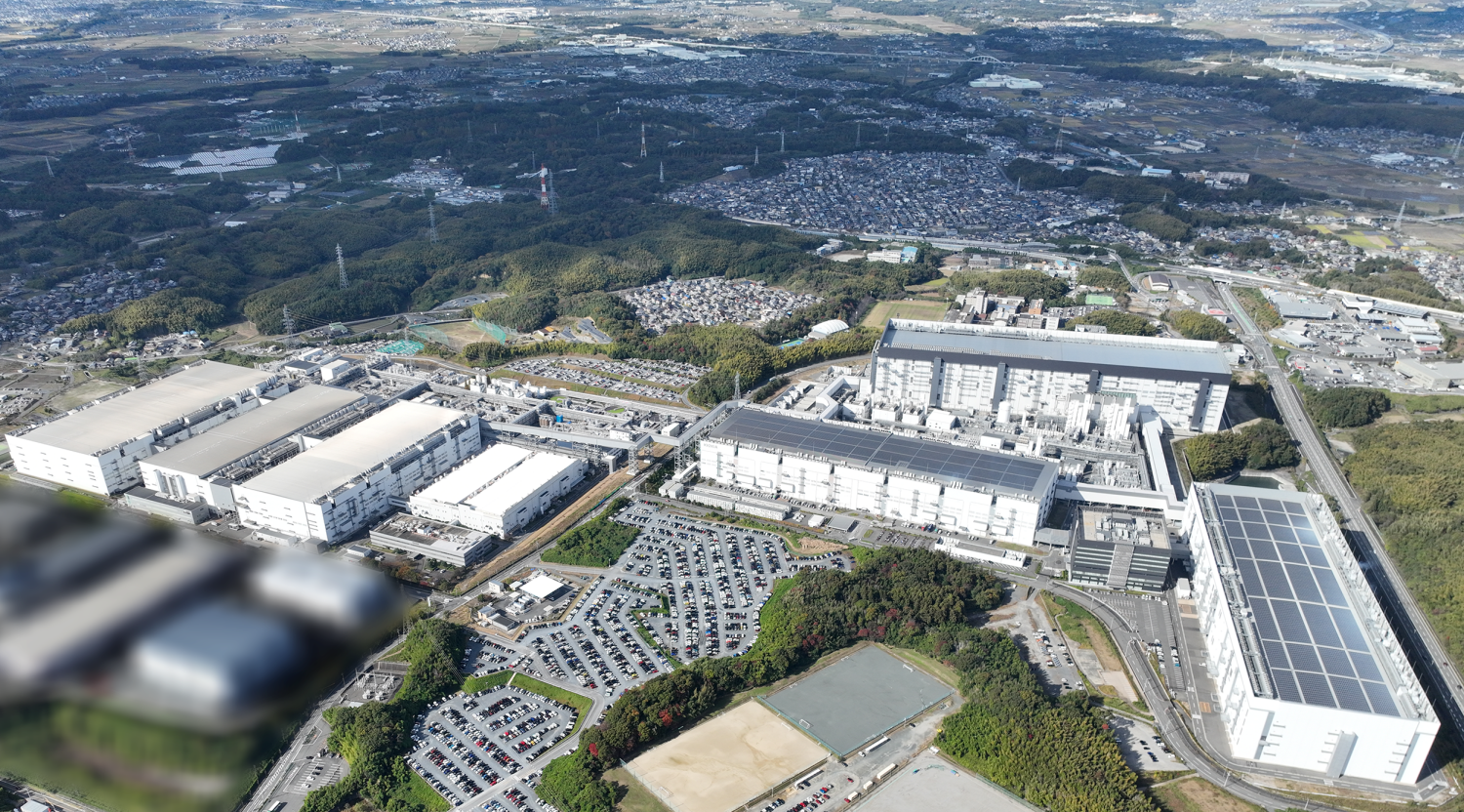
Panoramic view of KIOXIA's Yokkaichi Plant. (Source: KIOXIA)
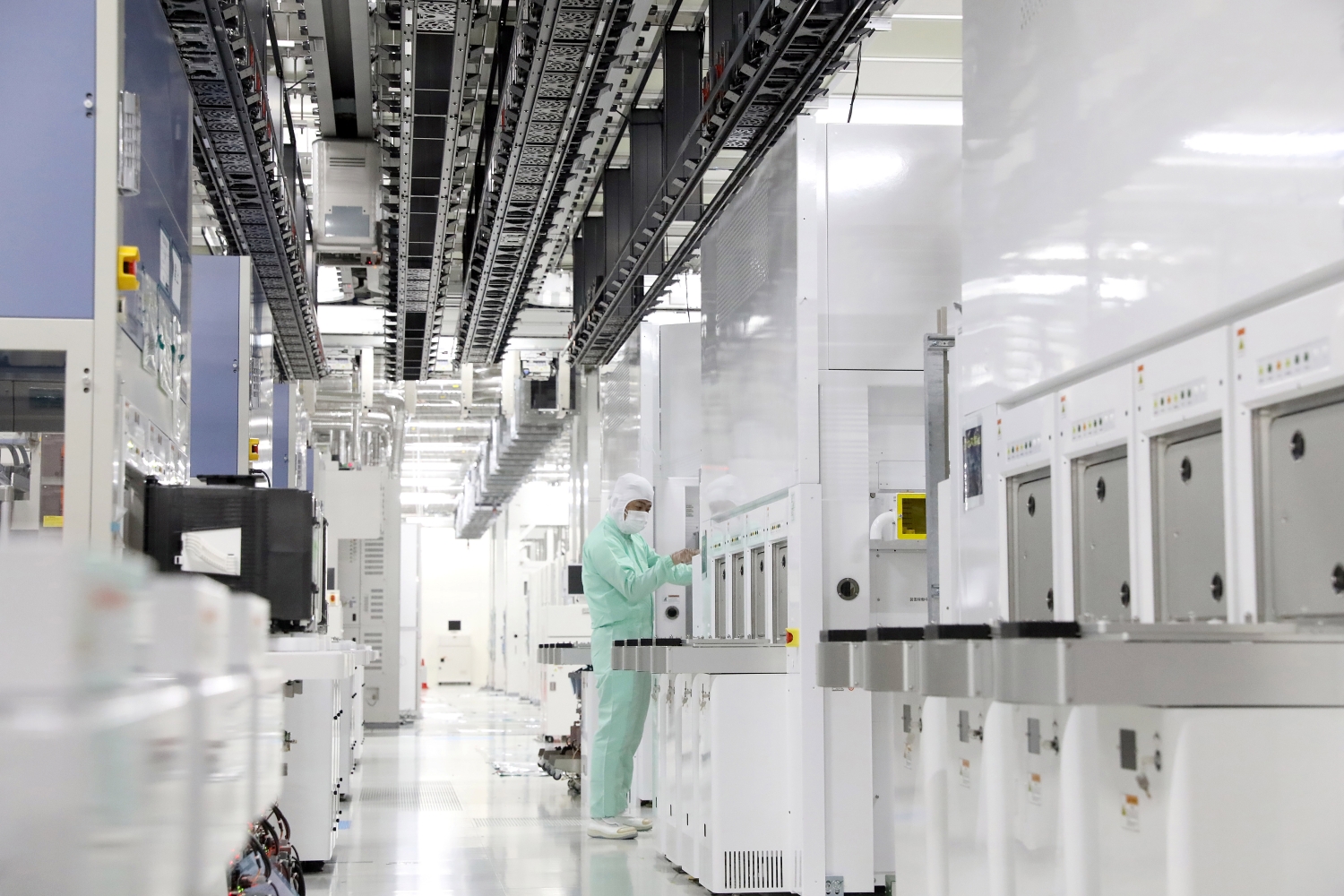
Inside a clean room of the Yokkaichi Plant. (Source: KIOXIA)
When the skilled expertise of engineers is not enough, smartification is born of necessity.
KIOXIA's stated mission is to “uplift the world with ‘memory’”. The company invented flash memory in 1987. Since then, flash memory has been adopted as a means of storing large amounts of data on a variety of electronic devices and systems including portable music players, digital cameras, laptops, smartphones, and data centers. Flash memory continues to be at the center of the evolution of applications.
The demand for flash memory for use in mobile devices, especially smartphones, has grown remarkably, and the Yokkaichi Plant has continued to expand in order to meet the rapid demand increase in the mobile device market. At the same time, smartphones, which keep evolving with each new model, constantly require larger capacity, higher performance, and smaller and thinner flash memory. KIOXIA meets these demands through a variety of technological innovations by miniaturizing memory cells, making them multi-level, and stacking them in three dimensions. This led to dramatic improvements in capacity and performance (flash memory capacity, 256 Mb (mega bit) in the 1990s, has now increased to a maximum of 2 Tb (tera bit)).
On the other hand, the memory structure becomes increasing more complex as flash memory evolves, making it more difficult to manufacture. In KIOXIA's latest product, BiCS FLASH*1 3D flash memory, more than 200 memory cell layers are stacked to a height of less than a few micrometers, and the memory cells have holes with diameters of 100 nm, the same size as the influenza virus, with a density of 10 billion per square centimeters. Furthermore, the uniform membrane found inside the holes has a thickness of 2 to 3 nm, the same width as DNA. For KIOXIA’s BiCS FLASH 8th generation 3D flash memory, the CMOS circuit wafer and the memory cell wafer are created under separate processes, and the two wafers are bonded together with high precision using CBA (CMOS directly Bonded to Array) technology. The bonding is controlled with such precision that if the diameter of the wafer were 1 km, any misalignment would amount to 1 mm or less. This type of extremely fine, precise manufacturing conducted at the Yokkaichi Plant requires no less than atom-level control.
Moreover, processed wafers are manufactured 365 days a year with no interruptions at the Yokkaichi Plant. Ensuring thorough quality control in the production of flash memory, where errors can be at the magnitude of a single atom, requires analyzing huge amounts of data, visualizing defects and areas for improvement, and immediately providing feedback to the manufacturing line. This is no longer a task that can be performed by engineers by means of skilled expertise based on knowledge and experience. Amid the hundreds of manufacturing processes, the amount of data generated by manufacturing equipment, inspection devices, and wafer transport systems is at 3 billion data points per day. This is far more than any human being can analyze. "That is precisely the reason why the Yokkaichi Plant has been proactive in introducing automation, IT, and the use of AI," emphasizes Kazuhiro Shimizu, Ph.D., General Manager of KIOXIA's Yokkaichi Plant.
Quality control based on 3 billion data points and AI
Since its establishment approximately 30 years ago, the Yokkaichi Plant has continued to expand in scale by adopting advanced digital technology, demonstrating a thorough commitment to smartification. The Plant had already achieved a high level of automation in its manufacturing processes 20 years ago in 2005.
That is not to say that the introduction of smart technology and AI proceeded smoothly from the very beginning. When the factory was established at the dawn of the Internet era, communication speeds were very slow, making data collection and analysis extremely difficult. Data originating in each production facility were stored in different databases, making it difficult to standardize and visualize. Still, it was far more efficient than having engineers analyze it manually. Through repeated trial and error and by incorporating cutting-edge digital technology, the Yokkaichi Plant became an incredibly smart factory. "As IT evolved, the efficiency of data collection and analysis improved dramatically. The evolution of flash memory also benefited from the evolution of IT," says Shimizu.
In addition to the highly automated cleanrooms, the Yokkaichi Plant collects 3 billion data points from all locations every day and analyzes them in real time using AI. The use of AI enhances the various types of analyses, including automatic estimation of the cause of defects by machine learning and image classification by deep learning, as well as to visualize issues and areas for improvement. The analysis results are immediately fed back to devices and systems and then incorporated into the manufacturing process. This makes it possible to thoroughly improve productivity and quality control and manufacture highly efficient, high-quality products.
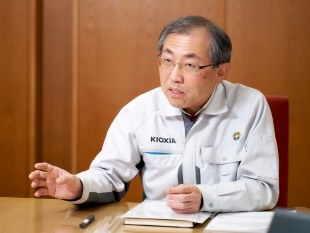
Kazuhiro Shimizu, Ph.D., General Manager of KIOXIA's Yokkaichi Plant
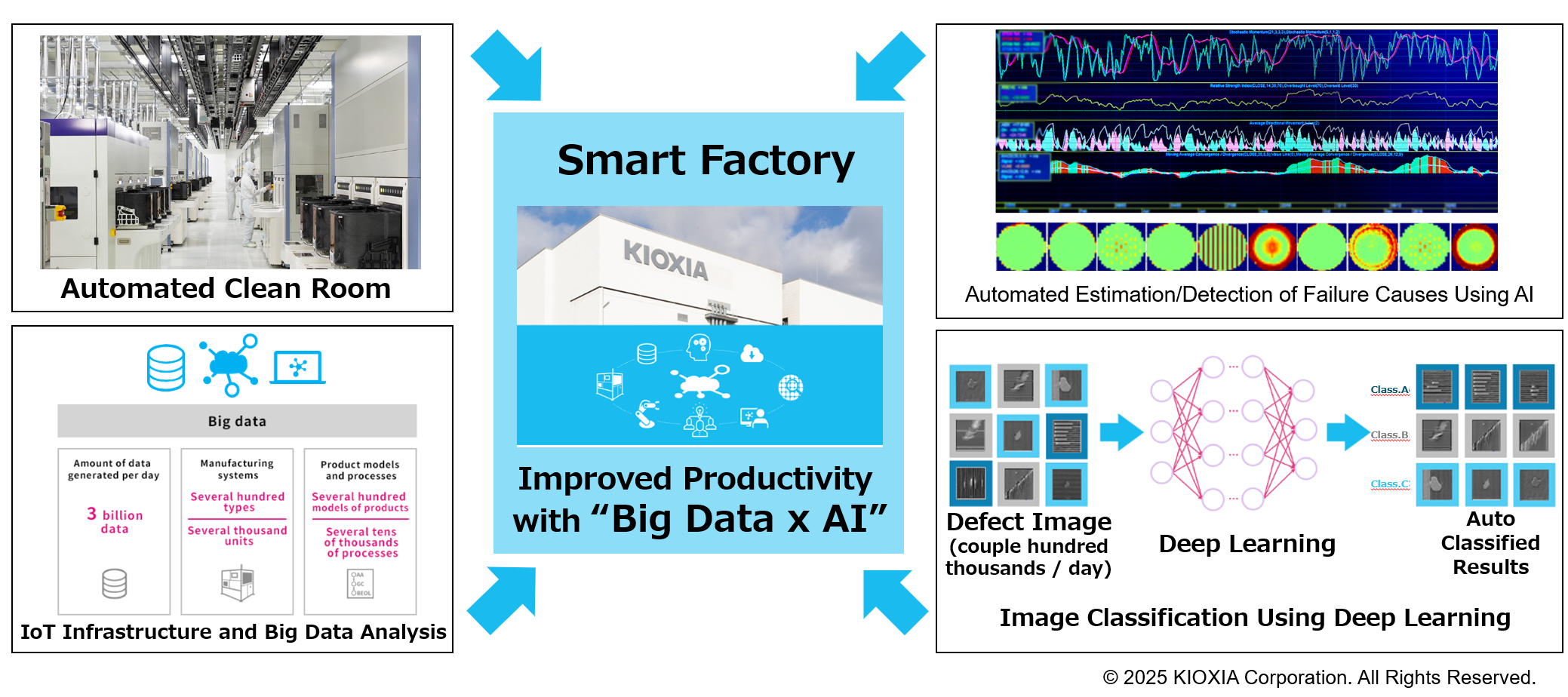
The Yokkaichi Plant’s cleanrooms operate under advanced automated control, and big data is analyzed in real time using AI, making it a state-of-the-art smart factory. (Source: KIOXIA)
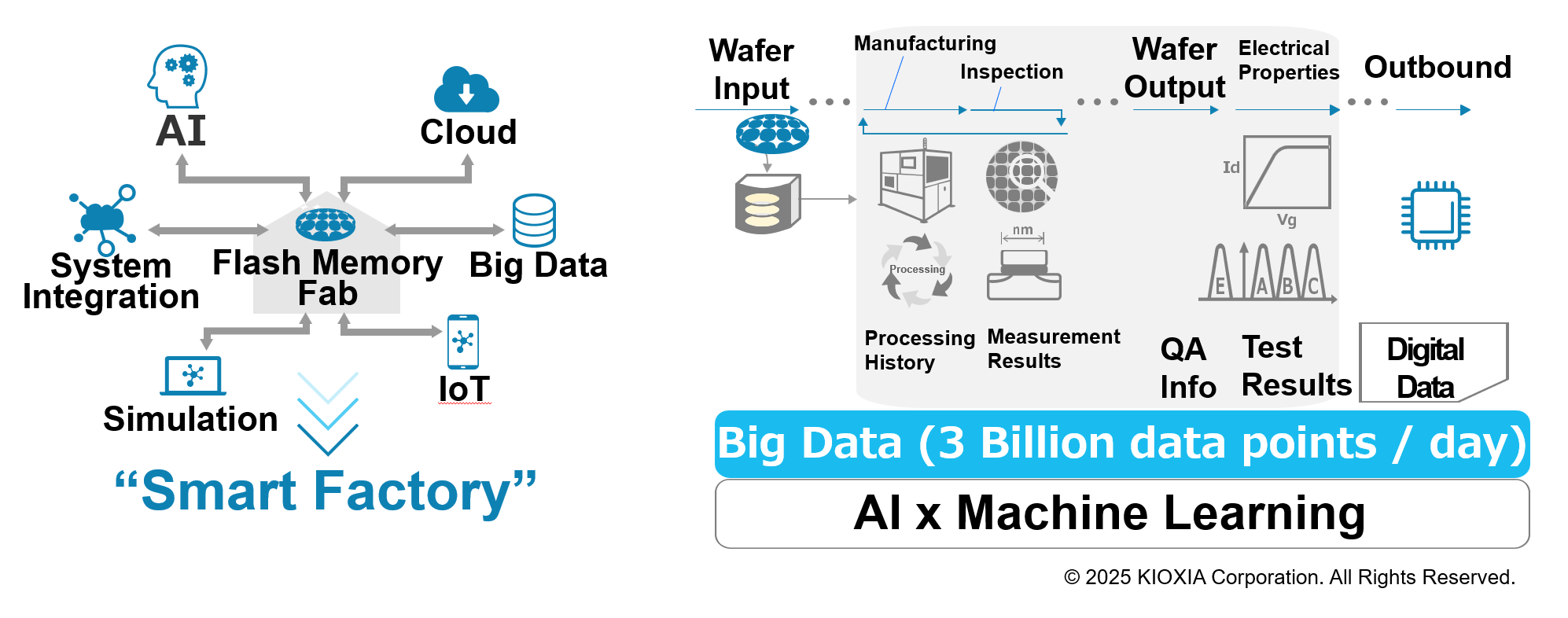
At the Yokkaichi Plant, quality is controlled in real time by analyzing big data using AI technology. (Source: KIOXIA)
"Engineers are entering a phase where they must consider how to utilize AI while developing products," says Shimizu. Indeed, at the Yokkaichi Plant, engineers are deepening their knowledge of AI by studying it on a daily basis. Engineers often devise and develop a variety of different AI applications necessary for high-quality manufacturing, including the advanced forms of analysis described above. There are also projects underway to circulate such knowledge among the engineers at the Yokkaichi Plant. "While it’s important to use IT and AI to aim for higher productivity, it’s the employees working here that are the real backbone of the factory," says Shimizu, emphasizing that it is engineers who built the massive smart factory that is the Yokkaichi Plant, and it is they who will continue to propel it forward.
Digital-twin technology, a fundamental step in the further evolution of smart factories
Just as KIOXIA's smart factory has incorporated state-of-the-art digital technology, the Plant is now about to evolve even further through the use of digital-twin technology.
Digital twins recreate real-world environments in a virtual space in real time, perform simulations and analyses, and then incorporate the results in the real world. Since this makes it possible to improve development efficiency and reduce costs, they are gradually being introduced into the manufacturing industry as well.
KIOXIA immediately turned to digital twins, and they are being used to promote collaboration between the Yokkaichi Plant and the Kitakami Plant (Kitakami City, Iwate Prefecture), which has been mass-producing flash memory since 2020. Recreating the Plants in a virtual environment in real time allows for the optimization of the manufacturing process by taking full advantage of the data obtained from manufacturing equipment and systems. Applying this procedure to the Yokkaichi and Kitakami Plants has allowed the Kitakami Plant to become operational in record time and to achieve a higher yield more efficiently than usual.
In the virtual factory space, all data related to manufacturing from the Yokkaichi and Kitakami Plants are collected in real time. "There are probably very few factories in Japan that use digital twins on such a large scale to carry out manufacturing," says Shimizu.
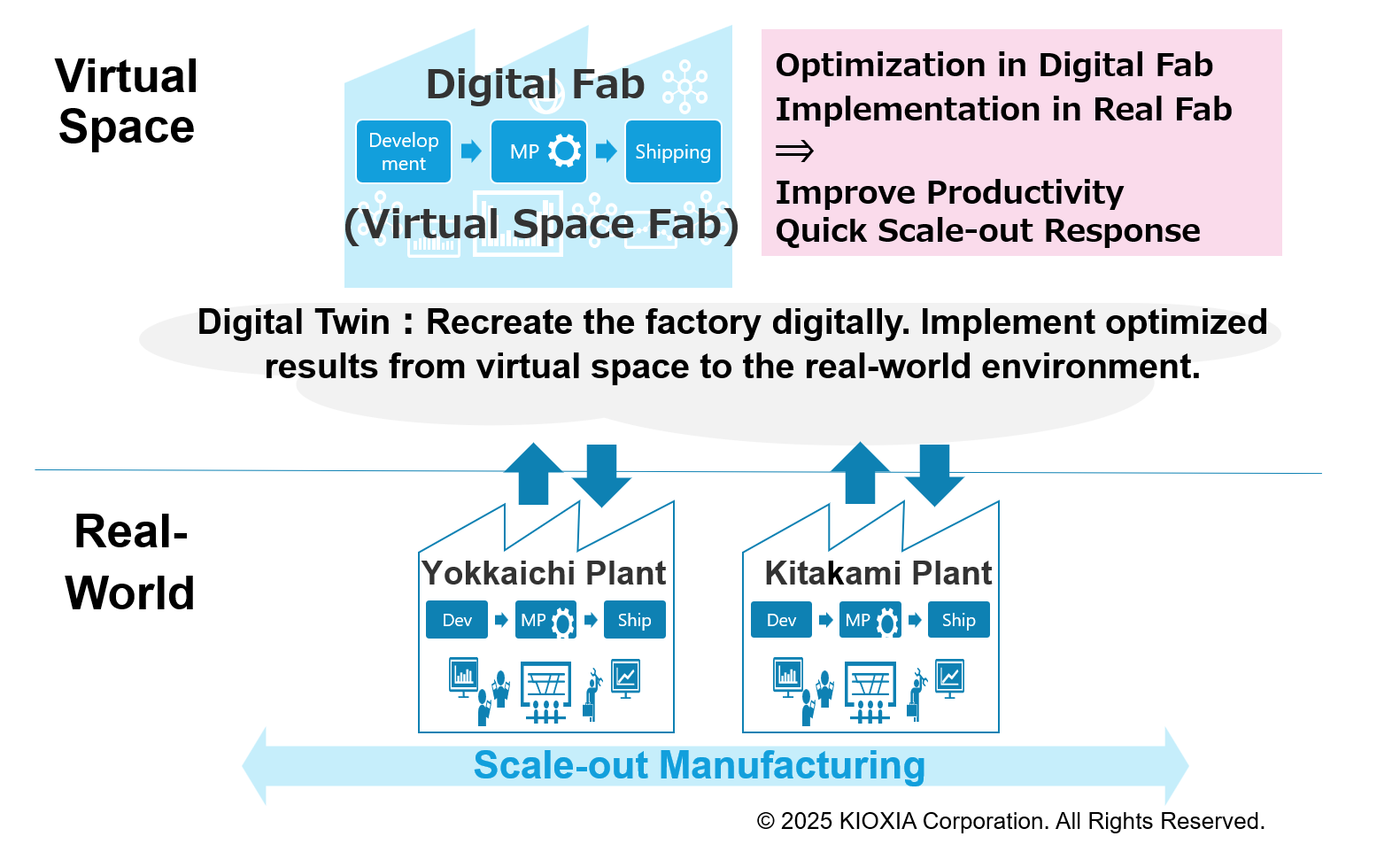
Linking different locations through digital twins. (Source: KIOXIA)
With its use of digital twins, the company is looking beyond manufacturing. By linking domestic and overseas manufacturing bases through digital twins, KIOXIA aims to not only speed up the creation and launch of products but also to optimize and strengthen the entire supply chain for the future from development to the procurement of materials and manufacturing and sales. Using digital twins to link all data from all manufacturing bases in real time will make it easier to assess production volumes and inventory levels, which will in turn help to optimize procurement of materials and raise the efficiency of sales activities. "The ideal we are working towards is to use digital twins to generate added value across the entire KIOXIA organization," says Shimizu.
Shimizu states that digital twins are a way to “redefine” the work. "The most important thing to ask is what your purpose is in using something. At the Yokkaichi Plant, AI is used in every department to increase the efficiency of work. However, this only means using AI to increase the efficiency of work as it is currently defined. We need to carefully consider how we can redefine and fundamentally modify work through digital transformation, of which the digital twins are one aspect. This will also lead to further development of our factories and KIOXIA's flash memory technology."
Towards a factory that continues to create added value
Since its establishment, the Yokkaichi Plant has continued to grow by incorporating new IT and AI technologies. "It will be important to see what kind of added value this Plant can create in the future. My dream is to combine semiconductors and flash memory, both of which the world needs, and provide them to make society and everyday life better," says Shimizu.
In terms of the development of a digital society, evolution is essential not only for CPUs and GPUs but also for flash memory. "If we use a human analogy, as people grow, their brains become quicker, and their memories improve. The combination of the two increases acumen. The same is true of a digital society; unless we improve both the performance of GPUs and CPUs, equivalent to mental agility, and of flash memory, equivalent to human memory, it will be difficult for the digital society to continue to develop. Flash memory needs to constantly evolve," says Shimizu.
As a constantly evolving smart factory, KIOXIA's Yokkaichi Plant will continue to provide the world with innovative flash memory that supports the development of a digital society.
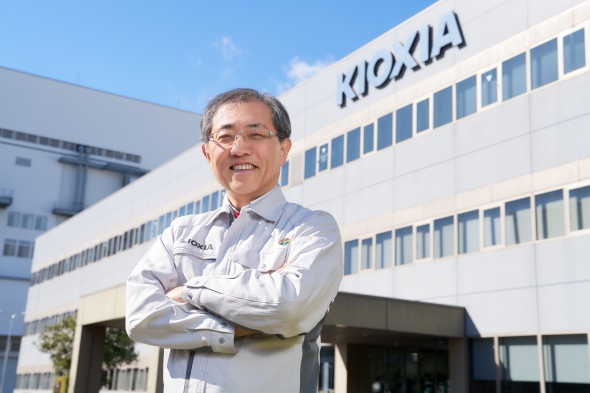
Notes
- The information described in this article is at the time of interview and may not be the most up-to-date.
- “BiCS FLASH” is a trademark of KIOXIA Corporation.
Please also check
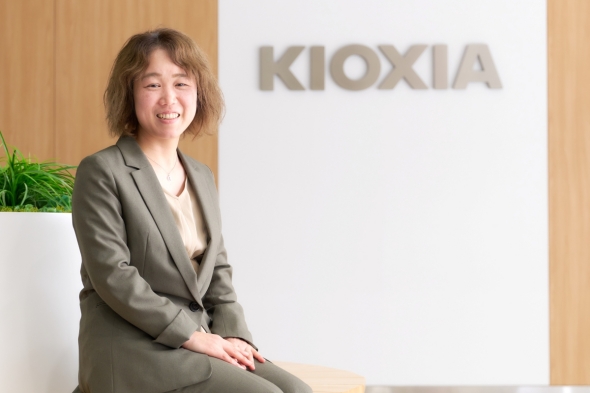
Building innovation on 3 billion data points and AI: KIOXIA’s Yokkaichi Plant takes on the challenge of state-of-the-art manufacturing
One of the world's largest flash memory factories, KIOXIA’s Yokkaichi Plant is also a massive smart factory that uses AI technology and the 3 billion data points it generates every day to manufacture cutting-edge products. While the use of AI is currently spreading across many different technology sectors, it has long been a standard part of operations at the Yokkaichi Plant. Here is a closer look at various initiatives promoted at the Plant, where many engineers understand and use AI to produce high-quality flash memory.