Please select your location and preferred language where available.
Building innovation on 3 billion data points and AI: KIOXIA’s Yokkaichi Plant takes on the challenge of state-of-the-art manufacturing
Making all engineers proficient in AI
Reprinted from: EE Times.com / EE Times.eu
Reprinted from content published in EE Times.com / EE Times.eu on July 21, 2025
This content is used with permission from EE Times Japan.
Department names and titles are as of the time of the interview.
One of the world's largest flash memory factories, KIOXIA’s Yokkaichi Plant is also a massive smart factory that uses AI technology and the 3 billion data points it generates every day to manufacture cutting-edge products. While the use of AI is currently spreading across many different technology sectors, it has long been a standard part of operations at the Yokkaichi Plant. Here is a closer look at various initiatives promoted at the Plant, where many engineers understand and use AI to produce high-quality flash memory.
In this massive smart factory, AI is already the norm
Seven production facilities stand next to each other on a vast area the size of about 98 soccer fields (694,000 m2), housing thousands of large machines that operate 24 hours a day in massive cleanrooms under advanced automatic control. Overhead, a great many automated wafer-transport devices move back and forth on rails, endlessly transporting wafers from machine to machine.
This is KIOXIA’s Yokkaichi Plant, one of the world's largest flash memory factories. Located in Yokkaichi City, Mie Prefecture, the factory has steadily grown since its establishment in 1992 to meet the rising demand for flash memory driven by the emergence of new applications. The Yokkaichi Plant currently employs approximately 10,000 workers.
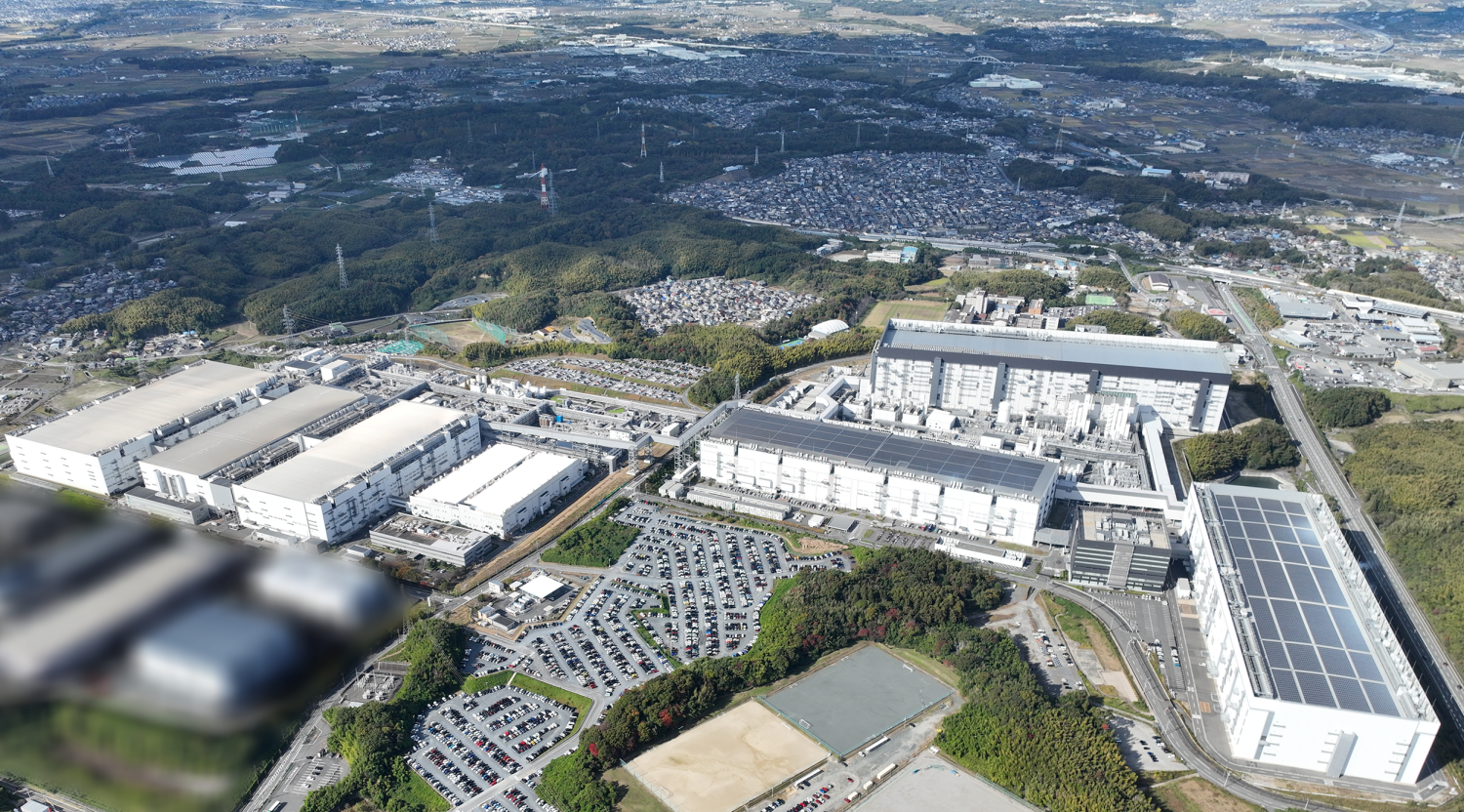
KIOXIA’s Yokkaichi Plant. (Source: KIOXIA)
The Yokkaichi Plant is defined by more than its colossal scale. Since its establishment about 30 years ago, the Plant has steadily evolved into a smart factory by integrating cutting-edge digital technologies. Smartification is the result of the proactive introduction of automation, IT, and AI - so much so that the Plant was already producing flash memory under advanced automated control as early as 20 years ago. In the mid-2010s, the Plant began to make full use of machine learning. Today, the Plant employs AI to analyze the 3 billion pieces of “big data” generated daily from all of its production facilities for use in producing high quality, high value added flash memory.
Japan’s manufacturing industry has been criticized for its slow adoption and use of AI in its business activities, so why does the Yokkaichi Plant routinely use AI? The answer lies in KIOXIA's unique approach of using AI to its advantage.
Three billion data points are the driving force behind AI
At the Yokkaichi Plant, the enormous volumes of data generated daily have been the driving force behind the introduction of AI to its operations.
The Yokkaichi Plant is equipped with several massive cleanrooms where data is generated from every corner, including manufacturing equipment, inspection equipment, wafer transport systems, and the cleanrooms themselves. As Yukako Tanaka, an engineer from Manufacturing Engineering Department II at KIOXIA’s Yokkaichi Plant explains, "The entire lifecycle of wafers, from the moment they enter the cleanrooms through the manufacturing process to the moment they leave as finished products, is converted into data." Every tiny piece of information (such as what day and time a certain wafer was processed, which manufacturing equipment was used, and what the settings of the equipment at that time were), is acquired as data. Furthermore, a large volume of data is also output in the course of evaluating manufactured flash memory, and detailed testing is performed down to a single bit. As a result, the Yokkaichi Plant generates 3 billion data points every day. Because the scale of data exceeds what engineers can manually process, the Yokkaichi Plant has been leveraging AI since an early stage to enhance the efficiency and speed of data analysis.
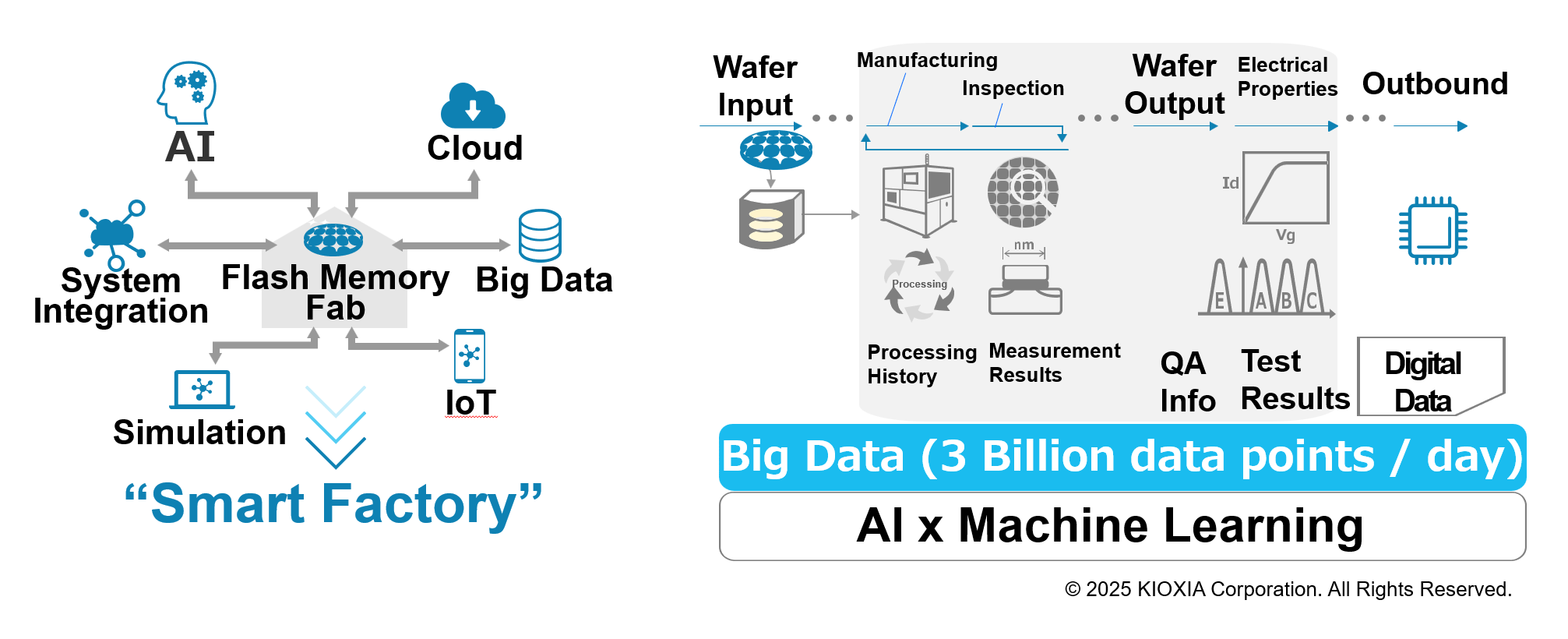
The Yokkaichi Plant is a smart factory that was an early adopter of automation and AI. (Source: KIOXIA)
Automating the defect identification process through AI reduced the analysis time by 99%
One instance of how AI is used at the Yokkaichi Plant can be seen during the quality management process. In this context, AI is used to analyze the data obtained from inspecting all devices (flash memory) and the data obtained from the manufacturing process (manufacturing equipment) in order to identify the causes behind defects. Modifying the manufacturing process so as to eliminate defects helps stabilize flash memory quality and improve the yield at the same time. You could say that AI connects device quality to manufacturing.
Consider the following example: when conducting device quality inspections, the company devised a unique method to automate the analysis of defects on the wafer surface using machine learning. More specifically, nonnegative matrix factorization (an AI technology for automatically extracting features from data) is used to quickly and automatically extract and classify the characteristics of defects and assess the distribution of non-conforming products. In the past, engineers would have to compare the data obtained from inspecting each wafer to determine and classify the characteristics of defects. Given the enormous volume of data involved, this would require a considerable amount of time. By achieving high-speed automatic analysis with the help of AI, the company succeeded in reducing the analysis time by 99%.
As for the manufacturing process, statistical modeling (Bayesian modeling) is applied to data analysis to determine optimal control values (such as device settings) for quality control, and a method has been devised to control the manufacturing process on the basis of those control values.
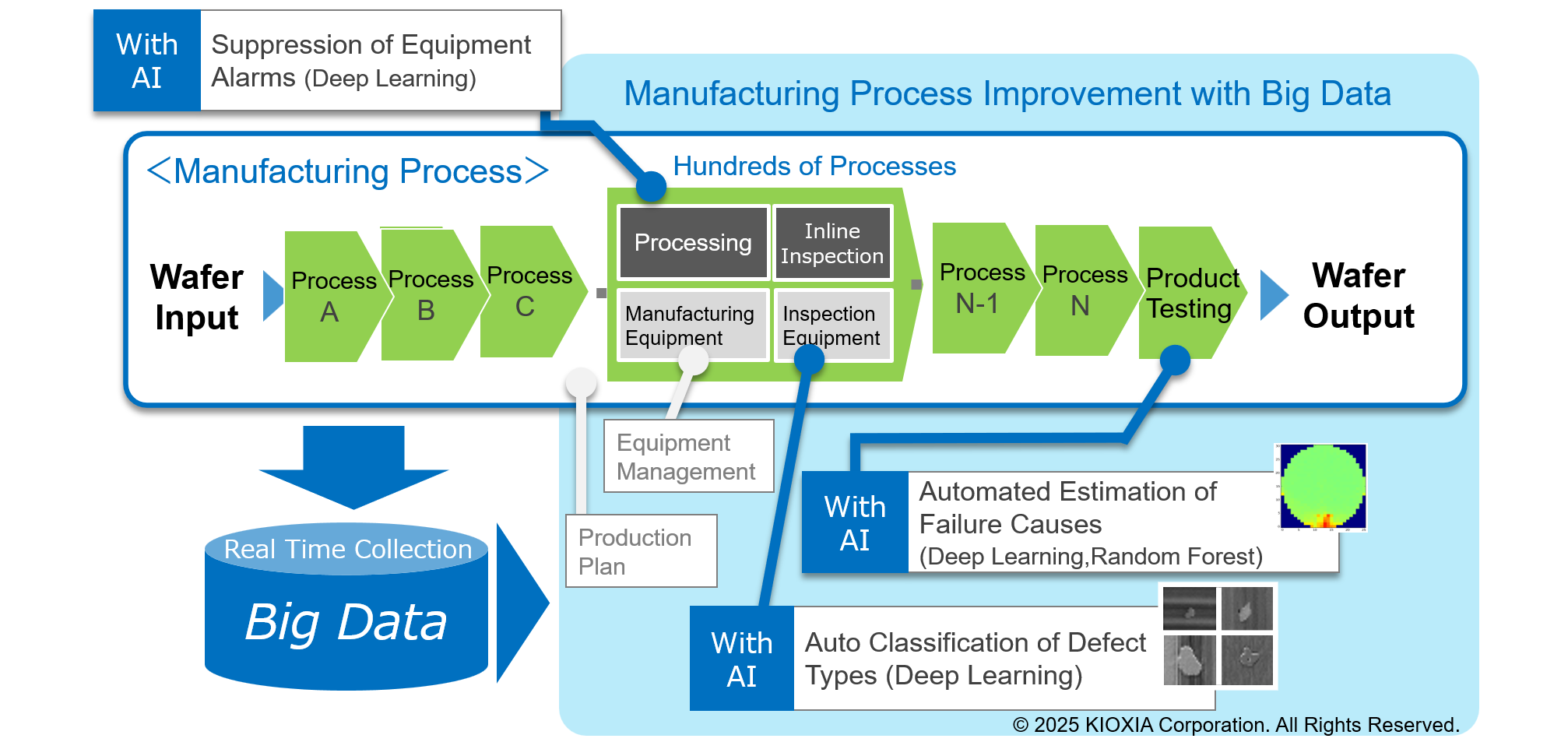
An example of using AI to improve the semiconductor manufacturing process. (Source: KIOXIA)
The method devised by Tanaka's team won numerous awards at international semiconductor conferences, including at the International Symposium on Semiconductor Manufacturing (ISSM).
Logical quality control through AI
One of the goals that the Yokkaichi Plant hopes to achieve is logical quality control based on data. This means being able to determine, on the basis of logical reasoning backed by data, how to change the settings of the manufacturing equipment in order to produce higher quality flash memory with a higher yield.
Interpreting the data that forms the basis of quality control has traditionally been the domain of engineers - relying on their experience and intuition. As mentioned above, failure analysis of the devices and manufacturing processes is heavily dependent on the know-how of experienced engineers. "However, in order to create something new, you have to compete in areas where you have no experience and where intuition doesn't work. That's why we've decided to go for logical quality control backed by data," says Tanaka.
While the intuition of experienced engineers is definitely important, Tanaka says, "The answers coming from intuition are not logical and contain many ambiguities." At the Yokkaichi Plant, using logical methods powered by AI to eliminate ambiguities allowed the engineers to make more efficient use of the knowledge accumulated over the years. Automated analysis, which reduced the analysis time by 99%, is a good example of this. Tanaka herself emphasizes how proud she is of such a great achievement.
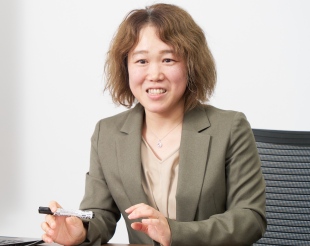
Yukako Tanaka, process integration engineer, Manufacturing Engineering Department II of KIOXIA’s Yokkaichi Plant
Tanaka uses AI for two purposes. The first is synthesis. AI is able to simplify and clarify the enormous volume of data generated at the Plant—3 billion items. This is also where AI is at its best.
The second goal is to make uncertainty visible. Flash memory production involves processing wafers at the nanometer level. Essentially, the manufacturing process proceeds at levels where the human eye is unable to determine what is happening. Furthermore, data related to failures is inevitably scarce since there are generally few failures. Therefore, the ability to extract information with as high a degree of certainty as possible from that sparse data is extremely important. In solving such a difficult problem, the value of AI lies in helping visualize uncertainty, in other words, expressing uncertainty in numerical terms.
“This would not be possible if you had to rely solely on an engineer’s intuition. It has only become possible with the advances in data analysis made possible by AI. If we can feed highly reliable results back into the manufacturing process, improvements can be made more quickly. AI gives us the materials on which to build decision-making," says Tanaka.
AI works like a magic filter
When explaining the use of AI, Tanaka’s favorite expression is, "AI is like a magic filter." "By passing the magic filter of AI over data, which are nothing more than strings of numbers and letters, you can extract new information. Data can be converted into the information you want. I believe this is how AI should be used," says Tanaka.
With new AI technologies and AI-based services emerging one after another, we have entered an era where the use of AI has become essential in all industries, including manufacturing. Many engineers and businesspeople might worry about not having the knowledge to use AI technology, Tanaka, however, says “I have never focused on the utilization of AI.”
"AI is merely one of the means at our disposal. To put it bluntly, I believe that you don’t need to use it if it is not necessary to achieve your goal," says Tanaka.
Tanaka, a process integration engineer, aims to clarify the relationship between devices and manufacturing processes in order to achieve logical quality control. For this reason, AI is only an option when identifying problems and considering methods to solve them. "In factories, they will traditionally tell you that you should not think in terms of means. You should instead consider the gap between goals and the current state of affairs and then come up with a map that connects the two. If there is an AI technology that can help you with that, then make full use of it," says Tanaka.
This is how Tanaka thinks the magic filter should be used. She also thinks that the filter should be as easy to use and as convenient as a magnifying glass. In order to turn AI into an easy-to-use tool for engineers, Tanaka has also been heading a project to promote the use of AI at the Yokkaichi Plant for several years.
From indifference to AI expertise
To familiarize employees with AI, the company launched internal projects consisting of holding workshops mostly aimed at young engineers to allow them to learn more about AI. At the end of the project, which may last several months to half a year, presentations are held with the help of visual aids, such as posters. Casual conversations with participants and engineers who just happen to drop by can sometimes lead to new opportunities for using AI. This is how the company is steadily spreading the use of AI.
This project, which started with just three people, has grown to the point where 200 people have taken part in the last two years. The AI seeds planted by Tanaka and her team have gradually sprouted and bloomed in different places within the Plant. "As a result of a series of internal projects, all of our engineers are now working with AI. I don't think there are many companies with such a high percentage of engineers proficient in AI," says Tanaka.
When it comes to familiarizing people with AI, Tanaka stresses the importance of two points. The first is the entertainment value. "Using AI is a lot of fun. I try to come up with projects that make people go, 'Wow! What is that? Let me try it!'" To that end, she even makes sure to give projects playful names.
The second point is that everybody must win—the creators who promote the use of AI like Tanaka and her team, the users who actually make use of AI, and the company that provides the required infrastructure to use AI, for example the IT environment. Tanaka insists that it is essential that all three parties obtain some benefits. No matter how advanced the AI technology you wish to use is, if the cost is too high, it will not be a realistic option for the company. It is, therefore, important to find the optimal solution in terms of the purpose of using AI, the quality of AI, its costs, and other such factors.
AI enables more freedom in your work
Tanaka thinks that AI is a catalyst for introducing more freedom in work and in the way of life in general. AI keeps evolving day by day, with new services being added almost on a daily basis. If you focus not only on the novelty of AI technologies but also on the purpose for which they are used, AI becomes an invaluable ally as the magic filter described by Tanaka.
While many are concerned that Japan is lagging behind in terms of AI, engineers at the Yokkaichi Plant have become very familiar with using it, which should dispel such concerns. KIOXIA’s Yokkaichi Plant is a smart factory that perfectly embodies the truth that AI is an ally to manufacturing.
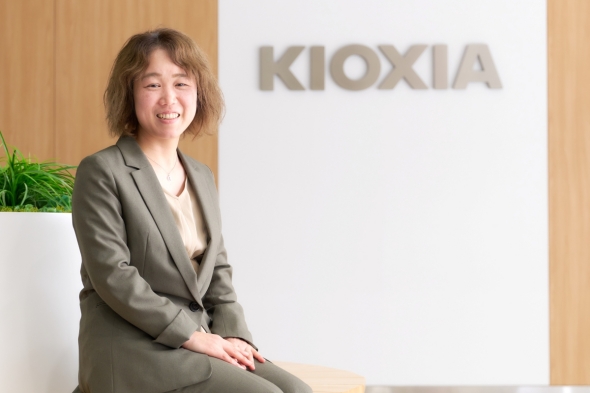
Notes
- The information described in this article is at the time of interview and may not be the most up-to-date.
Please also check
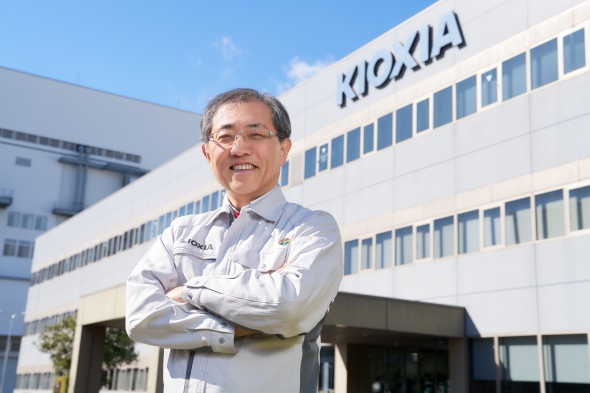
A massive, constantly evolving smart factory powered by three billion data points and AI: The Yokkaichi Plant of KIOXIA is at the forefront of flash memory innovation.
The Yokkaichi Plant of KIOXIA Corporation is located in Yokkaichi City, Mie Prefecture, one of Japan's leading industrial cities. In addition to being one of the world's largest flash memory facilities, the Plant is also a smart factory that has consistently introduced cutting-edge digital technology for the past 30 years. The Yokkaichi Plant manufactures state-of-the-art products by taking full advantage of AI technology and the 3 billion pieces of big data that the Plant generates daily, and it continues to further evolve through the use of digital-twin technology.